事例のご紹介
構内物流改善による生産性向上とコスト削減の両立
液体化学品の充填および出荷(ドラム缶・タンクローリー)および在庫管理を担当する部署において、取扱い製品の増大とともに煩雑化する管理業務を、「作業負担の軽減と管理精度の向上」(生産性向上)と「包材(ドラム缶)購入費の削減」(コスト削減)の観点で両立した事例。
問題点
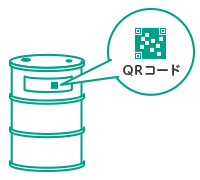
- 製品充填業務における問題点
同一ラインで複数品種の自動充填を行っており、また包材(ドラム缶・タンクローリー)の性質上、充填前に充填予定品種に合わせた事前準備が必要となり、作業員の業務負担が大きかった。 - 製品出荷業務における問題点
同一製品でも出荷先ごとに専用の仕様が存在していたため、仕様だけでも4,000種類以上あり、マンパワーによる物流品質の維持は限界を迎えようとしていた。 - 包材(ドラム缶)への直接表記(印刷)による包材調達コスト高
ドラム缶メーカーが品名・法定表記を印刷したドラム缶を購入していたが、取り扱い品目が多岐にわたるため、包材の在庫が多くなり仕様統一が求められていた。
改善施策
- 独自システム開発と導入
ドラム缶メーカーへの包材発注をEDI化し、包材製造時にQRコードの自動発行・自動貼付が行われるようにした。加えて、製品充填ラインにQRコード読み取りシステムを導入した。
これにより、充填監視作業が機械化され、チェック体制もシステム化されたことにより、ヒューマンエラー(人による判断)が大幅に削減できた。また各作業員IDを充填作業に紐づけることで、現場でのチェック作業の見える化(製品トレーサビリティ)も確立できた。 - 包材(ドラム缶)仕様の統一化
顧客の基幹システムの出荷情報を独自システムへ取り込むことにより、作業指示書および製品ラベルの自動発行が可能となり、約200種類あった包材を10種類にまで絞り込むことができた。
改善後の効果
- 経済効果
一元管理(充填~出荷)によるチェック、管理業務および受発注業務の効率化(作業工数約60%削減)
顧客の包材調達コスト(約4%)削減(ドラム缶へのマーキング廃止による合理化) - 副次的効果
作業員の感受性UPによる改善要求案の提出
「チェック作業の見える化」が図られたことにより、不満点も含めた現場からの生の声がシステムへフィードバックされる体制が構築され、システムの信頼性がより一層高まった。
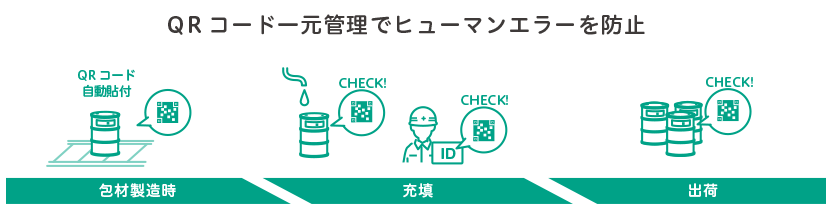
その他の事例
物流資材見直しによる積載効率アップと環境負荷低減
物流効率化と環境対応の両立(モーダルシフト推進)
物流にまつわるお悩み、お気軽にご相談ください。
お問い合わせ